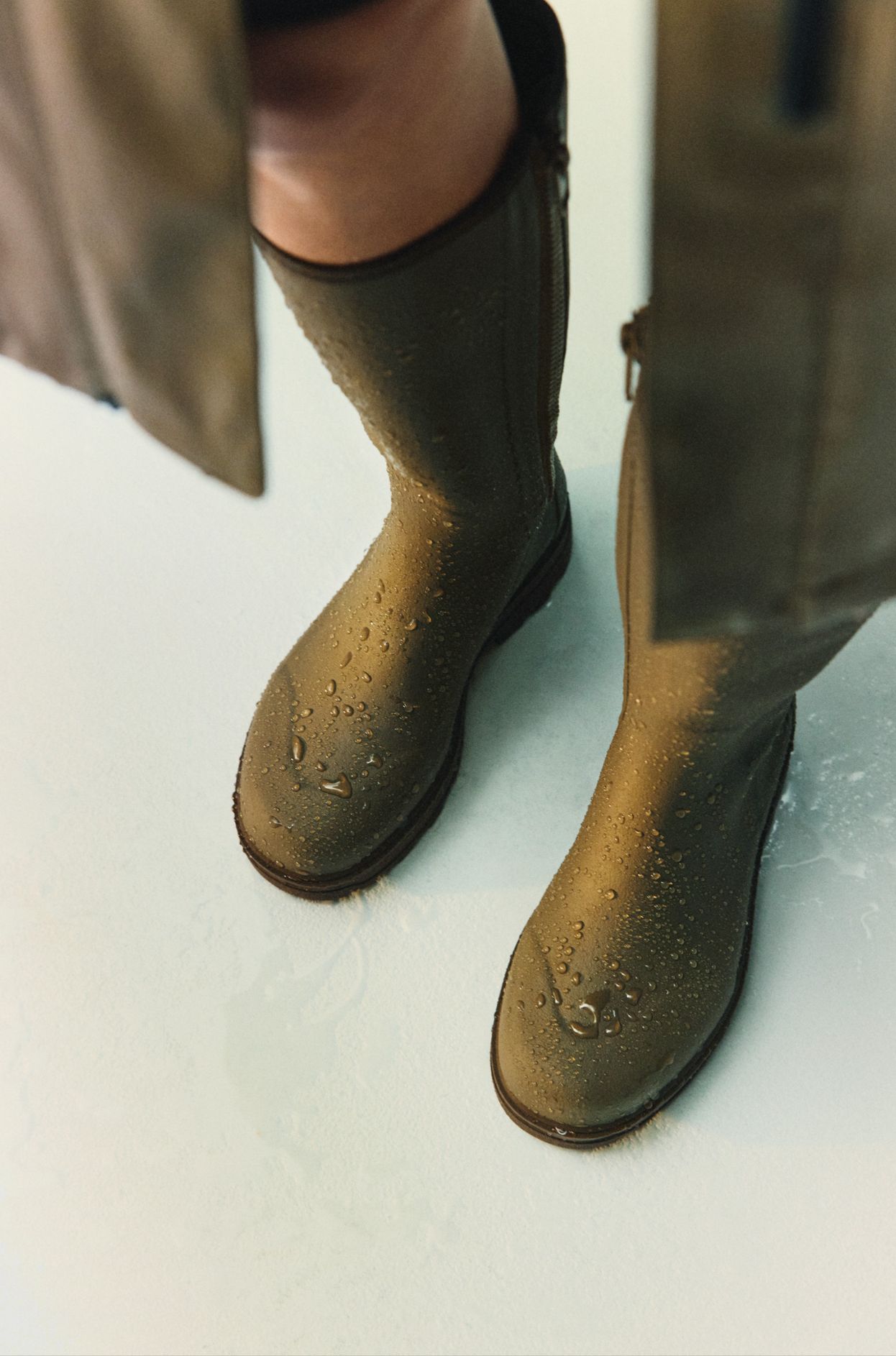
Journal
Explore the Tretorn world—where heritage meets innovation through collections, collaborations, and the ideas shaping our future.
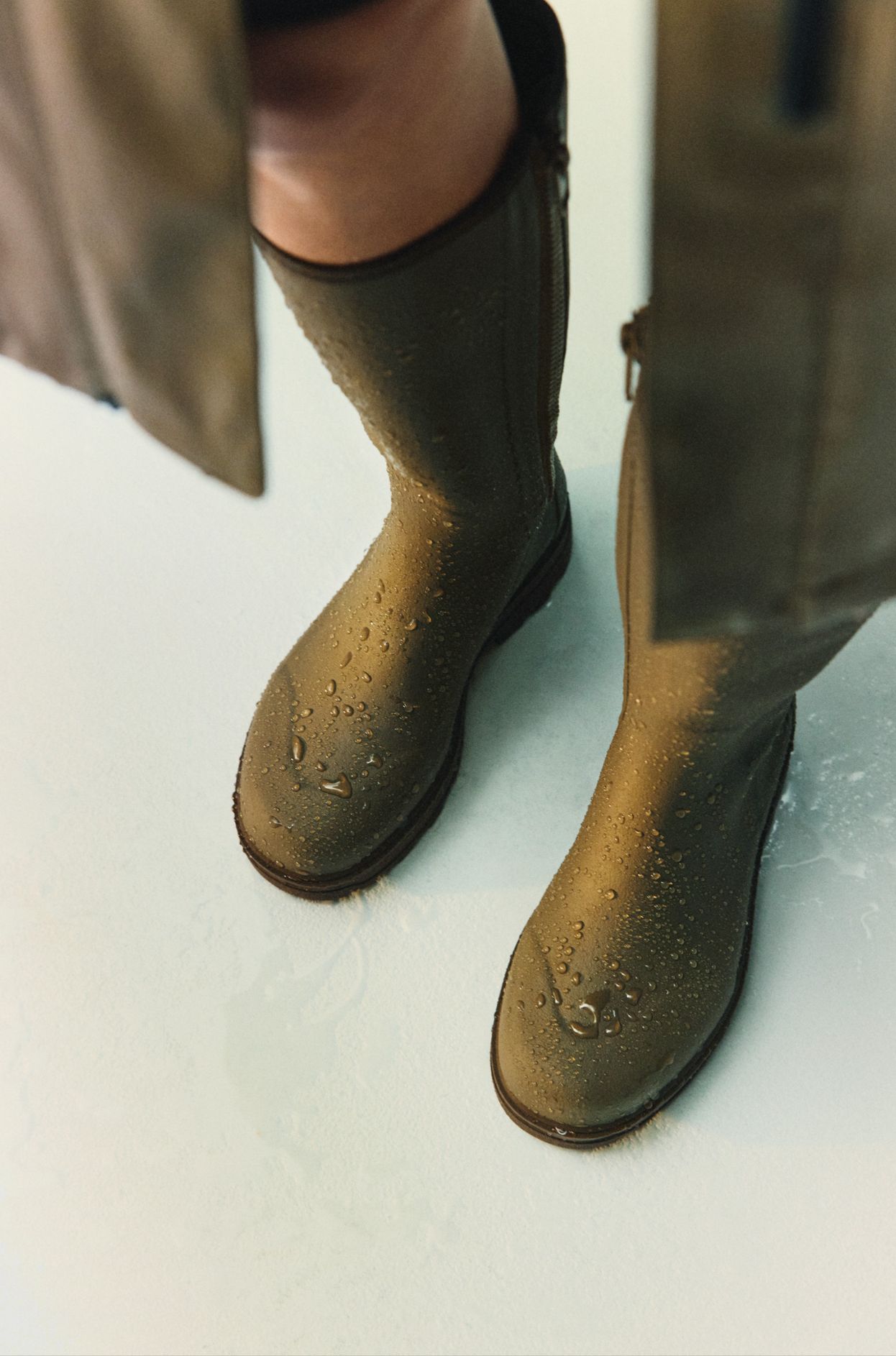
- 2024-10-21
- Collabs
- 5 min
Tretorn x KASSL Editions
The collection merges TRETORN’s heritage in rubber footwear with KASSL Edition’s captivating sense of functional contemporary style and comfort. It features eight styles capsule collection features premium rubber clogs, loafers, and boots, honoring both brands’ shared commitment to seamlessly transition between city and nature.
8 av 10 artikler